
Research


Rigid spur gear
Compliant spur gear


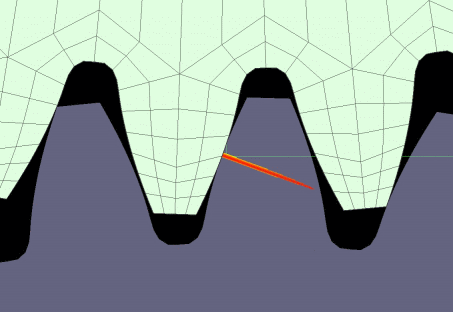
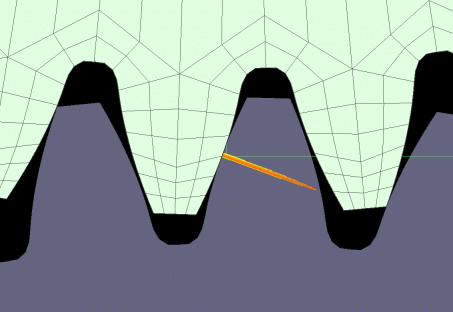
Coupled spur gear pair modeled using space-fixed mesh stiffness
Changing tooth contact
Tooth contact loss
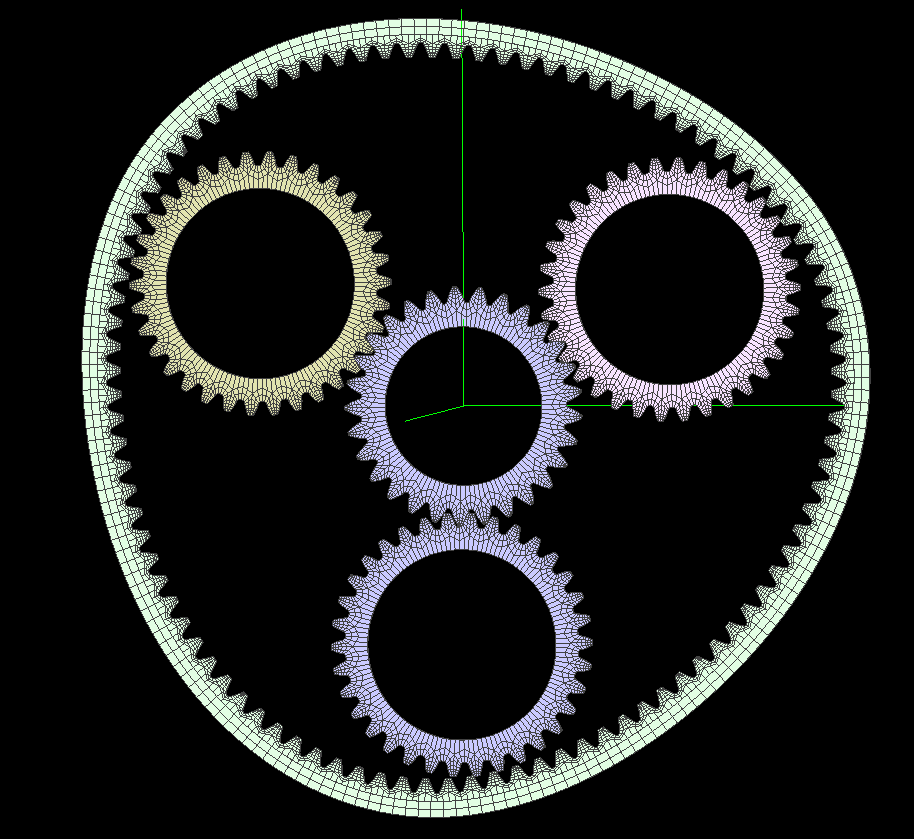
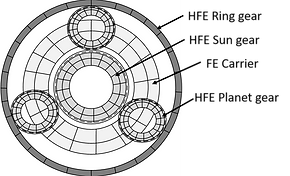
Planetary gear system modeled using semi-analytical model
Semi-analytical model to study vibration of rotating, coupled systems
(Ph.D. Dissertation)
Advisor​: Prof. Robert G. Parker, Virginia Tech
Conventional gears are rigid. Mainly for aerospace applications, to reduce
weight and increase efficiency, gears are made compliant.
Existing models based on multibody dynamics are not sufficient to analyze
these gear systems. Also, conventional finite element models lead to
time-varying models due to changing tooth contact points. Also,
three-dimensional FE models are computationally expensive. Thus, a
computational model to analyze compliant gears efficiently is being
developed.
Harnessing the axisymmetry of the gear body, Fourier series is used to discretize the gear in circumferential direction. This semi-analytical model reduces the 3D FE gear model to it's 2D cross-section models reducing the number of degrees of freedom and thus, computational time. The model includes rotational effects - gyroscopic, centripetal, and steady tension effects.
​
The semi-analytical model developed is used to study the natural frequencies and vibration modes. The contact between rotating gears is modeled as space-fixed mesh stiffnesses. Changing tooth contact between gear teeth is the main source of vibration in the gears. The dynamic analysis of gears due to changing tooth contact and contact loss is analyzed to obtain the excitation frequencies.
​
​
​
​
​
​
The semi-analytical model is extended to study planetary gear systems.
​
​
Nonlinear tuning and stability analysis of flexible rotor system
(B.Tech Project)
Advisor: Dr. Barun Pratiher, IIT Jodhpur (India) (Aug 2014- May ​2015)
​In this project, I developed a mathematical model of rotor system comprising of flexible shaft
and a rigid disk. The model incorporated higher-order deformation in bending to investigate the nonlinear dynamics. Multiple scales perturbation method was applied to obtain the nonlinear dynamic response of the system.
Different possible resonant conditions and resonant curves were examined. A parameter study was conducted to observe the variation of disk location, mass, and others on the dynamics of the system.
Comparative study of perturbation theory applied to nonlinear systems
Advisor: Dr. Sagar Chakraborty, IIT Kanpur (India) ​ (May 2016 - July 2016)
​
During this summer research, I was introduced to various perturbation techniques. I used Lindstedt-Poincare perturbation theory and Harmonic balance theory to derive the frequency for general nonlinear oscillators.
​
Hamiltonian formulation for conservative systems is essential in a variety of modern mathematical theories ranging from everyday-life Newtonian mechanics to esoteric high energy physics, from practical continuum mechanics to technical non-equilibrium statistical mechanics, etc. We developed Hamiltonian formalism for a class of nonlinear systems showing limit cycle behavior. The approach was inspired from Dual Bateman Hamiltonian formalism. Perturbation theories were then applied to study the damped simple harmonic oscillator (DSHO) and VanDer Pol Oscillator (VdPO)​. We have enriched this formalism by bringing non-conservative systems under its umbrella.
​
Design and analysis of power transformers (Crompton Greaves Pvt. Ltd.)
Supervisor: Sunil Gaikwad, Senior Design Engineer (May 2013 - July 2013)
​
During sophomore year summer, I worked at the Design Department at Crompton Greaves Transformers Div. Pvt. Ltd. in Mumbai (India). I got an industry experience during this internship and got to learn the functioning and processes involved in design analyses. Also, I got acquainted with the manufacturing processes involved.
​
I worked on computational testing of high power transformers and reactors. I conducted static structural and modal analysis on transformers to study the natural frequencies of the system. Also, I analyzed the stresses generated on the model during vacuum, lifting and jacking tests. These analyses were used to validate the transformer design and to modify it in case of high stresses. During the process, Siemens NX and ANSYS were used.
​
The computational results were experimentally validated by measuring deformations at various locations on the external transformer tank after a vacuum test.
​